
15 Dec Pressure Sensitive Labeling: Benefits, Applications, and Best Practices
Packaging is all about impactful branding or “shelf appeal” and pressure sensitive-labels offer a way for companies ranging from start-up to multinationals to have a great looking label with sharp, bright colors, finishes, and shapes to attract consumer interest.
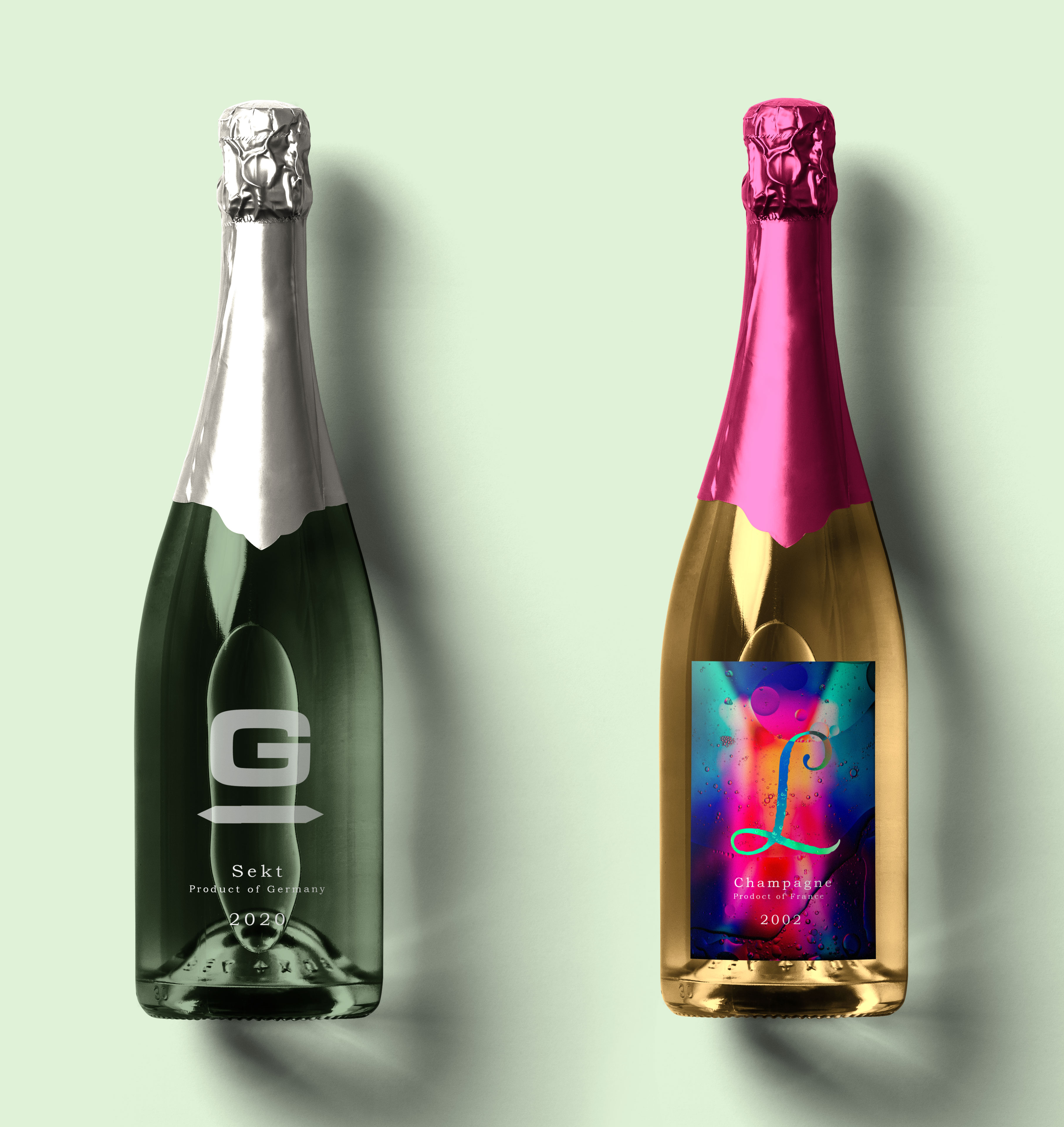
What is Pressure Sensitive labeling?
You could say that pressure sensitive labeling is a lot like stickers because unlike other technologies which require solvents or heat, P-S labels only require light pressure to fully adhere to most surfaces. They can be made of paper, film and foil and come in rolls and can be pressed onto a products by hand or using labeling machinery They can be produced in a variety of shapes and sizes, easily adhere to plastic, glass and metal, and can also be removed without much difficulty. With so many positive characteristics it’s not surprising that they account for 80% of all labels on the market today.
Advantages of Pressure Sensitive Labeling
First and foremost, pressure sensitive labeling are easy to apply and can withstand wet, cold, hot and dry environments which makes them very versatile. They can be used to brand rigid, flexible and some squeezable product packaging, and are ideal for achieving a no-label look. They are considered a “green” option because face stocks and liners are mostly recyclable and/or renewable. In addition, we see more and more linerless alternatives on the market. While such labels are limited to certain types of applications, they should be considered whenever possible.
Another great advantage to choosing pressure sensitive labeling is affordability. When compared with other labeling options they are among the less expensive choices and positively affect productivity due their ease of use, rapidity of roll changes and that cleaning is virtually unnecessary.

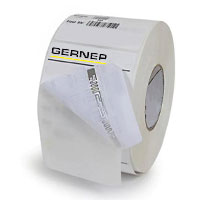
Pressure Sensitive Labeling Trends
Pressure sensitive labeling is already popular in many industries and are to stay. The appeal to these labels is growing globally as they are adapting to changing market trends. For instance, one emerging trend is Intelligent Labeling. RFID (radio frequency Identification) inlays which can be embedded to P-S labels as a way to collect and send information suck as tracking, storing and transmitting data.
Their sustainability is also an alluring characteristic which answers to consumers increasing ecological awareness. In many cases, the facestock used for P-S labeling is made of recycled materials and many of the adhesives used for their fabrication does not interfere with the recycling process.
Methods for Pressure Sensitive Labeling Application
There are three basic types of labeling methods used to apply pressure sensitive labeling: wipe-on, air-blow, and tamp-blow, however when working with rotary labeling systems it is most common to use the wipe-on method.
Wipe-On Method
With this method, the label is applied directly to the product and an additional roll or brush can be added to further “press” the label onto the product surface. The package and labeler speed need to be synced for proper application. This method allows the application of long labels as the product is moving while the label is being dispensed.
Air-Blow Method
This method uses vacuum to hold the label in place after being dispensed from the liner and dispenses it onto a tamp pad. The tamp pad extends towards the product and typically applies a light pressure to affix the label. The typical application for tamp-on is to apply labels to a recessed area on a product or apply small labels; a good example would be the label at the tip of cosmetic products such as lipsticks or mascara.
A slightly different device can be used as an alternative, which we call a tamp-blow. The same principle applies, but as the vacuum tamp gets close to the product, the air pressure that holds the label on the pad is inverted, and the label is blown on the product. This procedure is considered a no-contact application.
Tamp-Blow Method
This method uses a burst of air to blow each label onto the package as it passes by the applicator and does not require speed synchronization. Air-blow applications are typical where label placement accuracy is not critical, such as in produce packaging or meat packs where the surfaces can be uneven. It is also used where a label applicator is mounted on a transverse system where the movement is going back and forth to apply small individual labels across a web of film, for example.
P-S Labeling Recap
In conclusion, Pressure-Sensitive Labeling has evolved greatly over the past years and continue to rise to market trends. It is a great option for precision and adherence to most surfaces – even tricky ones. It offers a great level of performance and strikes a perfect balance between cost, efficiency, and brand appeal.