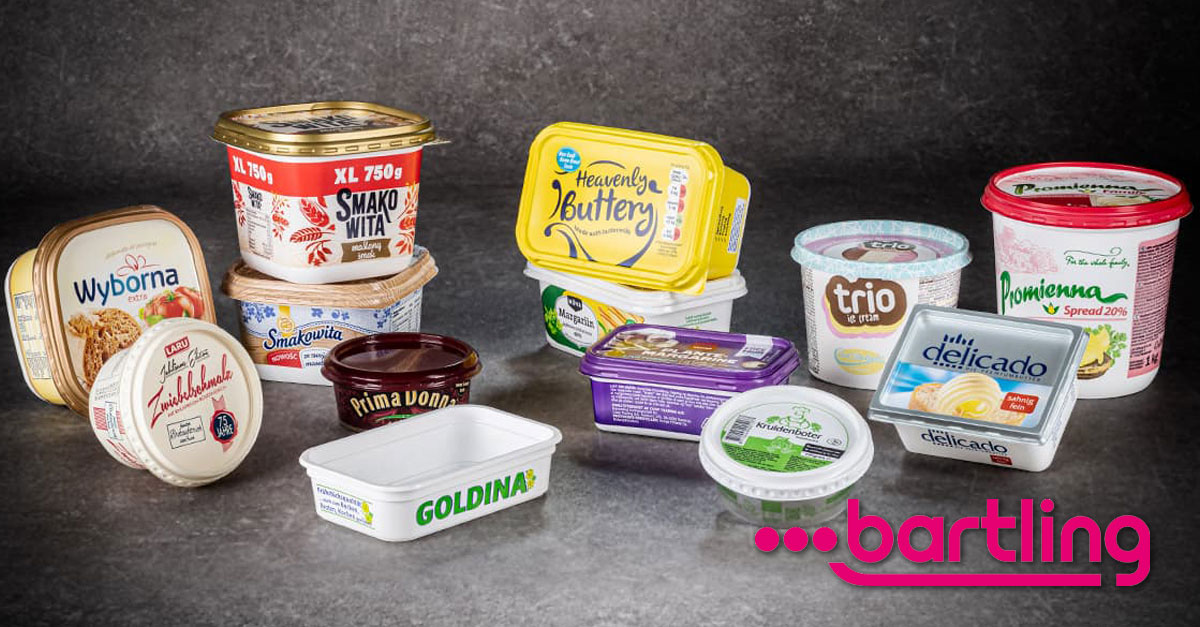
04 Aug Bartling Trusts Gernep for Modernizing
Modernizing and Selecting the Right Labeler
The automated process to apply pre-printed labels is a highly efficient one, offering unparalleled cost and time efficiency. Pre-printed product labels are available in different formats, including pressure-sensitive rolls or glueless/linerless rolls or precut & stacked labels of various sizes.
Selecting the right type of labels & labeler invariably depends on the packaging and the environmental conditions in the packaging plant. For example, in most breweries the bottles will come out of the filling machine wet, in these cases cold glue labeling provides optimal adhesion. Now consider a packaging producer that manufactures & labels plastic containers for food processors in a relatively clean and dry environment, in this case pressure-sensitive technology is an optimal choice.
Modernizing Labeling Installations
Bartling GmbH, a specialist in the production of plastic packaging for the food industry, recently partnered with Gernep to modernize its packaging production and labeling line. Supplier for many recognizable brands, Bartling produces a variety of Polypropylene (pp) or Polyethylene terephthalate (PET) packaging with heights ranging from 40 – 70 m and diameters from 95mm to 123 mm. To enhance its outstanding reputation, the company had already broadened their product portfolio to include pressure-sensitive opaque or transparent (no label look) plastic cup labeling. They partnered with Gernep to rejuvenate their outdated line due to their expertise in high-speed labeling processes.
Because of its relatively short lead time for designing and manufacturing a new labeling system, Bartling shipped their existing cup stacker to Gernep headquarters. This way, the team could work with exact parameters and ensure that the machine was perfectly aligned with the existing stacking & destacking equipment. The Soluta, Gernep family of labelers for pressure sensitive labels, was equipped with three pressure-sensitive label heads adapted to processing paper and film labels. The labeler was designed for non-stop operation and to provide greater flexibility for front, back, and bottom labeling. It is also easily adapted for double-layer or fanfold labeling. Additionally, it will allow the packaging producer to convert the stacking and destacking unit for higher outputs should it be required in the future. The flexible concept will enable Bartling to react to customer requirements and changing market trends.
Modern Machinery for Complex Labeling
As Bartling continuously modernizes and expands its production, the choice of a system already designed for higher output ranges and the application of more complex label shapes will provide them with the latitude to increase throughput. Soluta’s circular design also provides them with increased accessibility and no-tool quick changeovers for both labels and bottle formats.
Packaging manufacturers’ main concern is reliability, versatility and of course impeccably produced packaging, because 90% of product appeal is based purely on aesthetics. Gernep’s Automated Labeling Systems’ rugged design and flexibility will allow Bartling to face new challenges that arise daily.
5 Label Designs We Are Obsessed With
We are obsessed with the ingenuity of these 5 product label designs that artfully convey the spirit of their product....
5 Temperature-Related Labeling Issues
Spoiler – Weather and temperature affect labeling! Here are 5 common temperature-related issues to help you troubleshoot your labeling issues....
5 things to know about labelers
Buying a new labeling machine can be a big investment depending of your production requirement. We hope to be able to demystify the different types of labeling systems and help you make a sound decision....