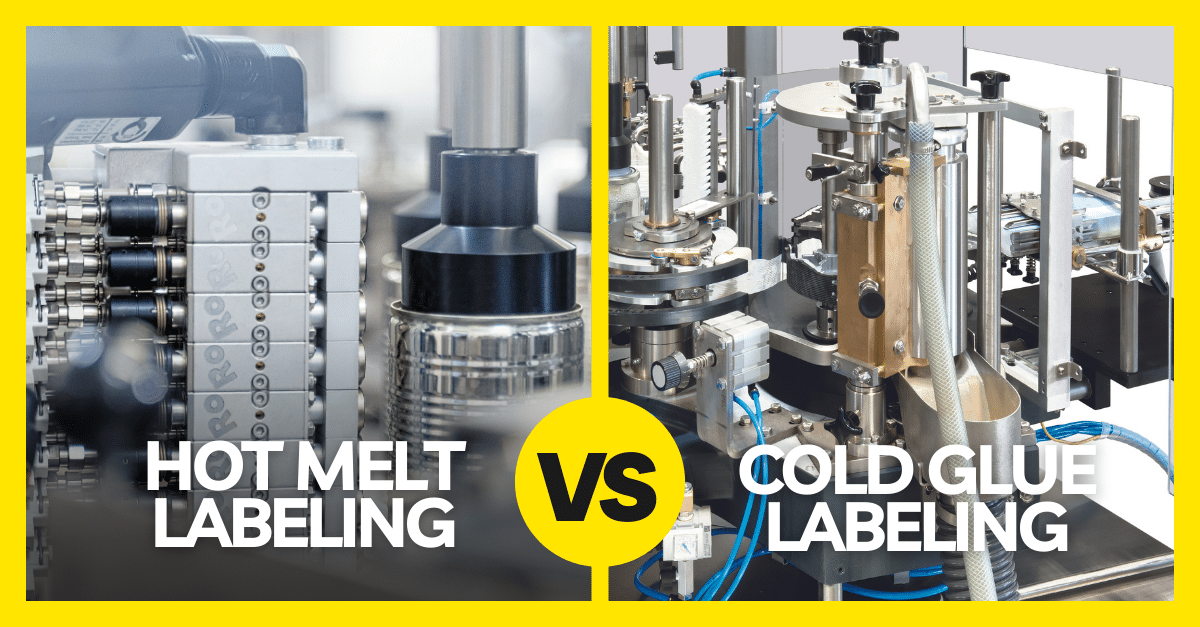
10 May Hot Glue vs Cold Glue Labeling: Expert Comparison for Rotary Labeling Machines
Hot Glue vs Cold Glue Labeling
Understanding the Technologies for Rotary Labelers
In industries packaging products, selecting the appropriate labeling technology is essential for ensuring manufacturing efficiency and quality. Two popular techniques are hot melt and cold glue labeling. At Gernep, we offer expert guidance in helping businesses find the right labeling solution. Let’s dive into what each technology offers and how they compare, enabling you to make an informed decision.
Understanding Rotary Hot Glue vs Cold Glue Labeling Machines
Rotary Hot Glue Labeling Machine: This machine uses a thermoplastic adhesive that is heated and applied in molten form. When the hot glue cools, it forms a strong bond, making it ideal for rapid and high-volume applications. The adhesive quickly sets, which reduces downtime and enhances productivity.
Rotary Cold Glue Labeling Machine: This machine uses a liquid adhesive that is applied at room temperature. It’s known for providing reliable and flexible labeling for various products. Cold glue is often chosen for its compatibility with a broad range of labels and containers, providing a sturdy bond.
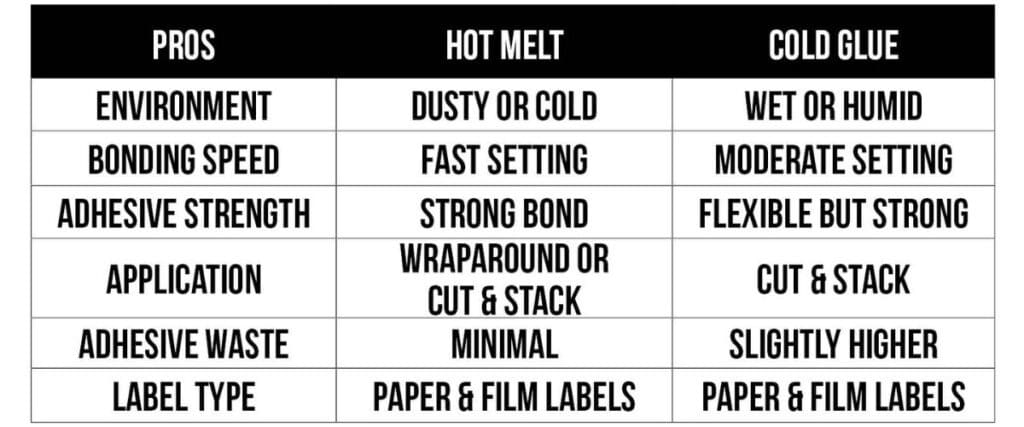
10 Key Considerations
When Choosing Between Hot Melt and Cold Glue Labeling Technologies
1. Cost Efficiency
Hot glue adhesives come with slightly higher upfront costs due to the specialized equipment and adhesive prices. However, they offer minimal adhesive waste and faster application speeds. On the other hand, cold glue systems have lower adhesive costs but may require more frequent maintenance and longer drying times. The choice between the two options should rest mainly on your container type and environment.
2. Application Method
Hot melt adhesives are contact-free, and the glue is molten, ensuring instant adhesion upon contact. Gernep’s hot melt system prevents penetration of condensation and maintains a precise temperature. Cold glue adhesives are applied at room temperature using rollers and pallets and are excellent for heat-sensitive materials. Gernep’s split glue scraper also allows for glue-saving application.
3. Container compatibility
Hot glue adhesives are highly versatile with film and paper labels, offering clean adhesion to plastic, glass, or metal containers. They are also suitable for full-wrap labeling. Cold glue works well with porous paper labels and a broader range of container shapes. However, cold glue struggles with high-sheen labels or non-porous surfaces, where the bond can be weaker.
4. Environmental Impact
Both adhesive types are developed with sustainability in mind. Hot melt adhesives produce minimal waste and can be recycled with other thermoplastics, although they often contain synthetic polymers. Cold glue, based on natural resins, is biodegradable and can be rinsed off containers for recycling. However, water usage for cleaning is a consideration.
5. Maintenance
Hot melt machines require cleaning the adhesive tanks to prevent buildup, while the nozzles and hoses must also be cleared of clogs. Cold glue systems require more frequent but straightforward cleaning due to the adhesive’s liquid nature. Maintaining the rollers or nozzles ensures an even adhesive coating during label application.
6. Performance
Hot glue adhesive’s immediate bonding makes it ideal for high-speed, and environments ranging in temperature from warm to cold. However, extreme heat can cause re-melting. Cold glue maintains its bond in most temperatures, is an excellent choice for adhesion to wet surfaces yet is sensitive to humidity and moisture, which can affect adhesion – think of beer bottles in a cooler.
7. Label Adhesion Issues
Challenges with Hot glue can often be attributed to a few issues like:
- greasy or wet container surfaces
- clogged nozzle du to overdue cleaning maintenenace
- viscosity due to insufficient heating of pellets
- mixing different adhesive grades in a tank
Challenges with Cold Glue can often be attributed to issues like:
- curved or textured container surfaces
- not oberving the glue grade’s service temperature range
- glue pallen insufficiently covered with glue
- labels have the wrong fibre direction
By thoroughly understanding each adhesive’s features, challenges, and best applications, manufacturers can select the most suitable labeling system that aligns with their production requirements and business goals.
Maximize Production Efficiency with the Right Labeling Solution
Tips for Buying Used Labeling Machine
Buying used labeling equipment can be a cost-effective solution that allows you to acquire high-quality machinery while saving money. However, it's essential to navigate the process wisely to ensure a successful purchase. Here are some valuable tips to consider when......
Rotary vs Linear Labeling Machines: A detailed Comparative Analysis
Explore the essential differences between rotary and linear labeling machines in our comprehensive analysis. This detailed guide covers speed, efficiency, versatility, and cost, helping you choose the right labeling solution for your business needs....
Maximizing the Labeling Efficiency of Unstable Containers with Puck Conveyors
Gernep Puck Conveyor Systems are specifically designed to maximize labeling efficiency for even the most unstable containers. Face the challenge head-on with Gernep and streamline your labeling process....