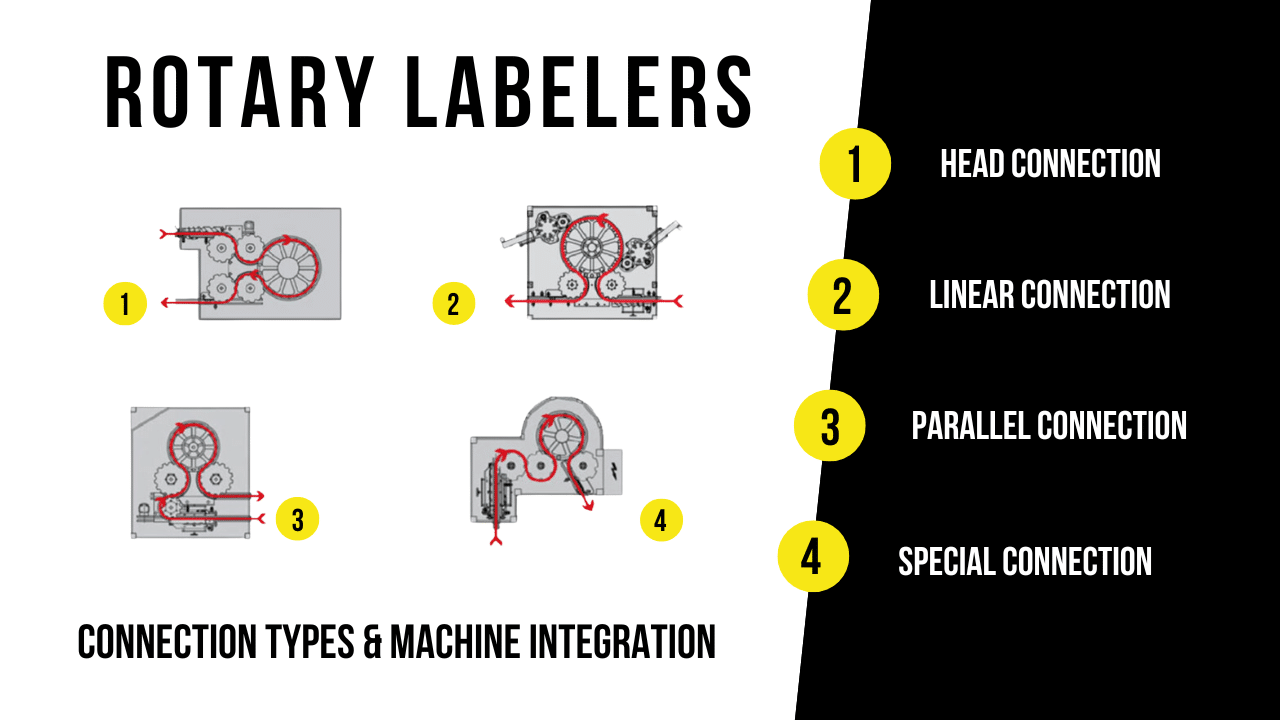
01 Feb Rotary Labelers: Connection Types & Machine Integration Rotary Labeling Machines
Optimizing Your Rotary Labelers for Production
Configuration, Connections, and Integration
Many manufacturers encounter retrofitting challenges when upgrading their equipment. However, the transition to newer, more advanced automated solutions can significantly enhance control over packaging operations, leading to improved efficiency and reduced costs. At GERNEP, we specialize in providing seamless replacements for underperforming labeling systems, offering you the opportunity to optimize your production lines with our high-value solutions.
When considering reconfiguring your bottling line, it’s beneficial to explore the various options available. One common choice is to replace inline labelers with rotary labelers. While the length of a rotary labeler is comparable to that of an inline labeler, it typically offers a wider design. This increased width, however, comes with the advantage of greater flexibility in positioning your bottle infeed and outfeed conveyors, making it a popular choice for speed requirements or complex applications.
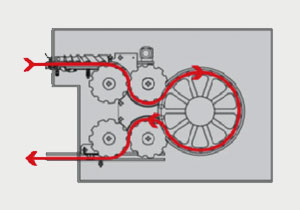
Head Connection
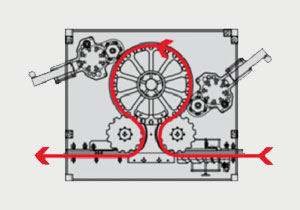
Linear Connection
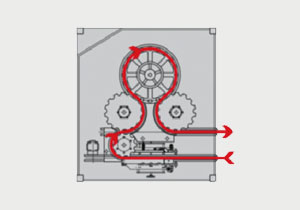
Parallel Connection

Special Connection
Strategic planning for the connection of new machinery to optimize floor space is a crucial factor that influences fluidity, bottle accumulation, and ultimately, total production output capacity and overall plant efficiency. Recognizing this, GERNEP offers a range of diverse configurations to assist customers in achieving the best possible results for their operations.
As part of our technical recommendation for your bottling line redesign, we suggest considering the purchase of a combination labeler. This technology allows for the incorporation of various labeling methods, such as pressure-sensitive, hot melt, or cold glue, into a single machine frame. This versatility enables the same machine to handle different bottle sizes, from small ones with front-and-back pressure-sensitive labels to large ones with cut-and-stack labels applied with hot melt.
Our rotary labelers, with their custom designs, are meticulously planned, configured, and installed to meet your immediate requirements. They offer significant advantages, such as minimizing assembly and reducing on-site downtime through extensive pre-assembly in our company, maintenance by our service teams worldwide, and ‘just in time’ service via remote diagnosis. These features are just a glimpse of how we ensure a successful partnership with you!
Butcombe Brewery Trust Gernep Machinery
Well known Uk Craft Brewer, Butcombe Brewery singles-out Gernep's Soluta, efficient pressure-sensitive machinery for it's home and co-packaging operations....
Maximizing the Labeling Efficiency of Unstable Containers with Puck Conveyors
Gernep Puck Conveyor Systems are specifically designed to maximize labeling efficiency for even the most unstable containers. Face the challenge head-on with Gernep and streamline your labeling process....
Rotary Labeling Technology Demystified
The right labeling technology can make a significant difference in your production line. In this blog we offer a comparison of the different labeling technologies available, so that you are selecting the right machine to get your job done as efficiently and cost-efficiently as possible....
Selecting the right beer labeling equipment for your needs
Efficient labeling equipment will dramatically increase productivity and pay for itself quickly by immediately increasing production....
The Evolution of the North American Beverage Industry
Adapt swiftly to North America's dynamic beverage industry with customizable labeling machines. Embrace market changes through enhanced flexibility, sustainability, and efficiency and stay ahead thanks to systems designed to ensure your operations are future-proofed......